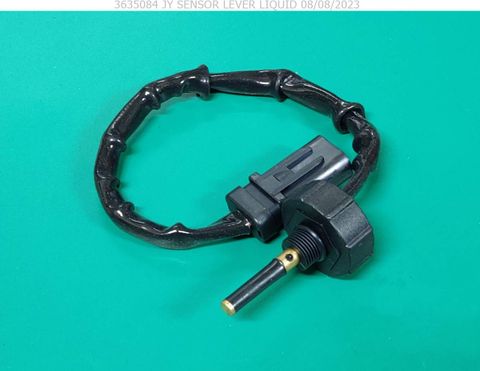
LEVER LIQUID SENSOR
கடைசியாக புதுப்பிக்கப்பட்டது
விலை:
R.F.Q
Share Product:
விவரம்
A non-functional lever liquid sensor, which typically monitors fluid levels in various systems of an excavator or other heavy machinery, can cause several significant issues affecting the machine's performance, safety, and maintenance. Here are common problems associated with a faulty lever liquid sensor:
Inaccurate Fluid Level Readings:
- False Low or High Alerts: The sensor may provide incorrect readings, indicating that fluid levels are too low or too high when they are not. This can cause unnecessary concern or complacency.
- No Alerts: If the sensor fails to detect actual low fluid levels, it may not alert the operator, leading to continued operation with insufficient fluids.
Component Damage:
- Hydraulic System Damage: Inaccurate readings from a faulty sensor can lead to running the hydraulic system with insufficient hydraulic fluid, causing overheating, increased wear, and potential failure of hydraulic components.
- Engine Damage: For sensors monitoring coolant or oil levels, failure can result in running the engine without proper lubrication or cooling, leading to severe engine damage.
Reduced Performance:
- Overheating: A non-functional coolant level sensor can fail to alert the operator to low coolant levels, leading to engine overheating and potential engine failure.
- Poor Lubrication: An inaccurate oil level reading can result in poor engine or transmission lubrication, causing increased friction, wear, and potential failure.
Increased Maintenance Costs:
- Frequent Breakdowns: Ignoring actual low fluid levels due to sensor failure can lead to frequent breakdowns and repairs, increasing maintenance costs and downtime.
- Unplanned Maintenance: Operators may need to perform unplanned maintenance or inspections to verify fluid levels manually, disrupting regular maintenance schedules.
Safety Risks:
- Operational Safety: Low hydraulic fluid levels can affect the responsiveness and control of hydraulic systems, posing a risk to operator safety and the safety of others on the job site.
- Fire Hazard: In some cases, insufficient fluid levels (such as oil) can increase the risk of overheating and potential fire hazards.
Operational Interruptions:
- Unreliable Operation: Without accurate fluid level monitoring, the machine may experience unexpected shutdowns or performance issues, leading to operational interruptions and decreased productivity.
Diagnostic Challenges:
- Troubleshooting: Diagnosing fluid level issues without a functional sensor can be challenging, requiring more time and effort to manually inspect and verify fluid levels.
- Misleading Data: Faulty sensor data can mislead diagnostics, potentially causing technicians to overlook the actual problem or misdiagnose the issue.
Warning Light Activation:
- Erroneous Warnings: The machine's warning systems may frequently activate due to incorrect sensor readings, causing operator frustration and potential neglect of actual warnings.
- No Warnings: Conversely, the absence of proper sensor function can lead to a lack of warning for critical low fluid levels, resulting in severe damage before the issue is detected.
Summary
A non-functional lever liquid sensor can lead to inaccurate fluid level readings, component damage, reduced performance, increased maintenance costs, safety risks, operational interruptions, diagnostic challenges, and warning light issues. Addressing sensor malfunctions promptly is crucial to maintaining the optimal performance, safety, and reliability of the machinery. Regular inspection and replacement of faulty sensors by a qualified technician can prevent these problems and ensure efficient and safe operation.
4o
விவரக்குறிப்பு
திறவுச்சொல் | |
பிராண்ட் | |
தோற்றம் | MY |
பட்டியல் Download